Taiwan’s TSMC is building a third chipmaking fab near Phoenix, Arizona, bringing its total investment in the state to $65bn. The project, subsidised by $6.6bn in Chips Act and Science Act funding, is the largest greenfield FDI project in US history. The facility will employ 6000 workers and create tens of thousands of indirect jobs. Beyond concrete and steel, the massive undertaking also requires robust investment in human capital to ensure its success.
The first fab was set to open this year, but last July the company announced delays caused primarily by a shortage of workers with the technical expertise to commission and operate the facility. It is now projected to begin production in the first half of 2025. Part of the problem is that the US lags its Asian competitors in semiconductor fabrication, leading to a domestic skills gap. While expertise in this field will eventually grow, the issue is broader, encompassing demographic and cultural factors beyond any single industry.
In January 1979, US manufacturing employment reached an all-time high of 19.6 million, representing 22% of non-farm employment. Over the next four decades, the sector steadily lost jobs, despite the civilian workforce expanding from 105 million in 1979 to 164 million in 2022. That year, roughly 8% of the workforce was employed in manufacturing.
As manufacturing jobs dwindled, Gen X (born between 1965 and 1980) were encouraged to work in other sectors like business services, education, health and hospitality. Many baby boomers (born between 1945 and 1965) were laid off in industries like textile, steel, electronics and automotive manufacturing. Those that remained have retired or are nearing retirement, taking their expertise with them. Gen X has a smaller workforce and fewer manufacturing skills. Millennials (born between 1981 and 1996) are a larger cohort than Gen X, but they too lack the technical skills needed for today’s highly advanced manufacturing. As a result, manufacturing operations like TSMC’s will face workforce challenges until the skills gap between retiring boomers and emerging Gen Z workers is bridged.
In the near term, the US should issue more work visas for foreign technical talent. In the medium term, investing in and developing technical training programmes is crucial. But solving the issue long term demands systemic and cultural shifts, plus patience, as we prepare the future workforce to meet the needs of today’s hi-tech manufacturing.
fDi
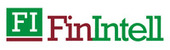